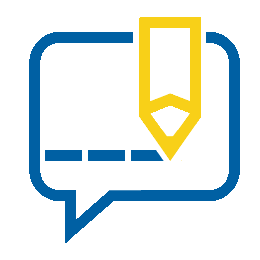
How to Avoid the High-Temperature (and Odorous) Exhaust Associated with Diesel Generators
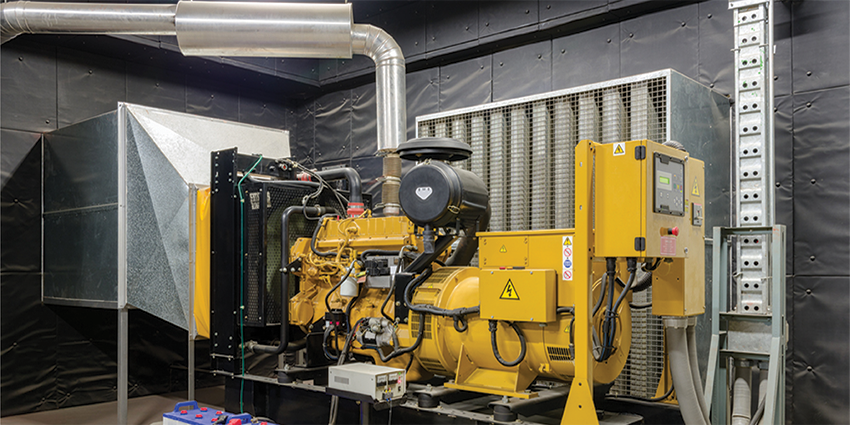
Electricity. Practically everyone uses it. We power everything from a children's toy to hearing aids using some form of electrical power. Electric power makes life productive and comfortable. Sometimes, it even saves lives.
However, what happens when the power is interrupted? For most, it's an irritation. Still, in some situations, it is the difference between life and death. The possibility of power interruption is why some applications rely on backup power. Hospitals, laboratories, data centers, and other mission-critical facilities almost always use backup power sources. These sources often are diesel-powered generators.
Diesel generators are fuel-efficient and run longer—helpful in the event of a long-term power outage. These generators, while providing life-saving electricity, also have a darker side.
The complaint against diesel generators comes from the high temperatures it produces, along with the distinctive smokey odor. This combination of a noxious odor and high temperature causes problems when the generator is operating. Placement of the exhaust stack and changing wind direction can cause the smoke, heat, and odor to re-entrain into the facility or a neighboring building.
One Solution
Most diesel generators are very heavy, often requiring placement on the lowest floor of a building. Generators can range widely in power generation capabilities depending on the use. For example, a 1500kW generator can produce 12,000 cfm of exhaust fumes. The temperature of those fumes can exceed 775°F.
Exhausting those fumes requires ductwork running from the generator to the building roof deck. The ductwork connects to an exhaust stack. The variables of exhausting these fumes often cause air quality issues inside the facility and neighboring buildings.
One solution to prevent re-entrainment uses extended roof stacks. The extended roof stack will place the exhaust higher above the roof deck. However, this solution does have its own set of challenges.
The Best Solution
The previous solution addressed the high-temp, odorous exhaust coming from a diesel generator. However, the additional cost, stress on the generator, and aesthetics make this solution a poor choice. The best solution allows the high-temp exhaust to enter a bypass plenum where it mixes with ambient air. (Figure 1)
![]() |
Figure 1 |
![]() |
Figure 2 |
Mission-critical operations such as those in hospitals and laboratories cannot be without power for extended periods. Diesel generators currently provide most backup options for these situations. However, these generators create high-temperature exhaust and diesel odors that can add cost and increase the potential for effluent re-entrainment.
The best solution addresses all these concerns, reducing the effect of high-temperature exhaust, ensuring no exhaust reenters the building or nearby facilities, and does so without affecting building aesthetics.
You can learn more about high-plume dilution systems for diesel generators and watch the following video to see the system in action.
from