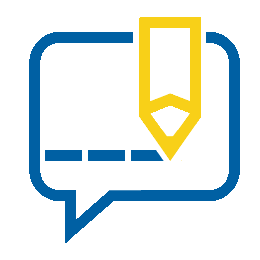
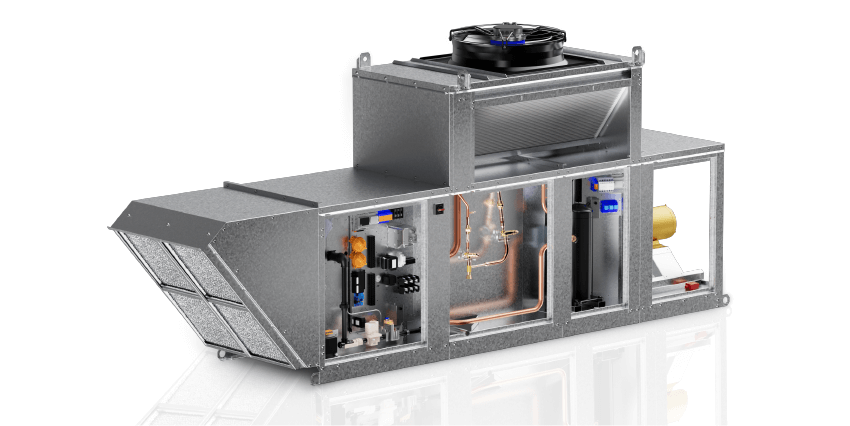
The transition from A1 refrigerants to A2L refrigerants effective January 1, 2025 has made a strong impact on the HVAC industry. Because A2L refrigerants have a low global warming potential, the change will make HVAC equipment less harmful to the environment, which is why the U.S. Environmental Protection Agency mandated it. But because A2L refrigerants can sustain a flame while A1 refrigerants cannot, this change also requires manufacturers to adapt their equipment to remain safe with no drop in energy efficiency or air quality. Learn how direct gas-fired make-up air units with direct expansion technology have been redesigned to keep commercial kitchens cool, warm, and ventilated.
Why Use Make-up Air in Commercial Kitchen Ventilation Systems?
When commercial kitchens are cooking, air filled with smoke and odor is continually being exhausted through the building’s roof. Make-up air makes up for that air, preventing negative air pressure from developing. Negative air pressure makes it difficult to open doors and makes the exhaust system more inefficient.
Make-up air is therefore required by building codes for commercial kitchens, such as the International Mechanical Code (IMC). Make-up air units available today can temper the air by heating or cooling it, keeping kitchen occupants comfortable. Because many choices for air tempering are available, building owners and engineers need to balance cost, efficiency, and employee comfort when choosing a make-up air system, without compromising on safety.
Direct Gas-Firing and Packaged Direct Expansion
Direct gas-fired make-up air units, such as Greenheck’s Model DGX, provide 100% outdoor air that is tempered by being heated over a gas flame. By contrast, indirect gas-fired make-up air units like Greenheck’s Model IGX fire a heat exchanger with a gas burner, and the air passes through the heat exchanger for warming.
Which type of system to use depends on the application and budget. Indirect gas-fired heaters are often used in sensitive applications such as hospitals where byproducts of combustion are not allowed, since the heat exchanger filters out and exhausts those byproducts. In commercial kitchen ventilation systems, direct gas firing is a common choice due to its lower installation and maintenance costs, its more precise temperature control, and its smaller equipment footprint.
Direct expansion (DX) cooling is available with both types of units. With DX cooling, heat is transferred through the evaporating and condensing of refrigerant (Figure 1). The refrigerant is compressed to a hot gas in the compressor and cools to a high-pressure warm liquid as it passes through the condenser coil. The expansion valve rapidly drops the pressure in the refrigerant, chilling it to a vapor saturated with droplets. As it passes through the evaporator coil, the refrigerant warms to a gas, taking heat energy out of the air.
![]() |
Figure 1 |
Packaged direct expansion (PDX) means that the components are in one rooftop unit. This differs from split direct expansion, where the evaporator coil and fans are inside the building and the compressor and condenser coil are on the roof.
Improving on Excellence
The industry-wide transition from A1 to A2L refrigerants has made safety a top priority for make-up air units that use direct gas firing to heat air and direct expansion technology to cool it. The new challenge posed is that refrigerant could leak into the open flame of the burner and combust. Given that this combination of HVAC technologies provides 100% outdoor air with 92% energy efficiency, however, it was important to design a unit capable of continuing to deliver these strong results safely.
![]() |
Figure 2 |
The innovative design of microchannel coils, which was pioneered by the automotive industry, allows for the coils to use 50% less refrigerant than standard coils and be 40% smaller.
Putting Safer Design to the Test
Product safety standards such as UL 60335-2-40 are important in the HVAC industry for ensuring that if refrigerant were to leak, manufacturers have designed detection and mitigation into their equipment. Greenheck has implemented mandatory requirements from the relevant standards and added safety features to address the risks. Intertek, a third-party tester, evaluated Greenheck’s redesigned DGX unit over several days. The testing found that the unit’s published power consumption was accurately rated. It also found that the additional safety features were operating at full effectiveness.
This success in testing demonstrates that a direct gas-fired make-up air unit with PDX cooling can continue delivering the benefits of tempered outdoor air along with the industry’s transition to A2L refrigerants.
Learn More
Find a Greenheck Representative: Find a representative in your area who can answer questions about finding the right make-up air solution for your application.
Direct Gas-Fired Make-Up Air Units: Browse Greenheck’s highly configurable offerings for making up air with burners that are capable of up to 30:1 turndown (the ratio of maximum to minimum heat output).
The Safety of A2L Refrigerants in Direct Gas-Fired HVAC Equipment: This white paper from Greenheck explores refrigerant safety testing with direct gas-fired equipment in more depth.
Make-up Air
from