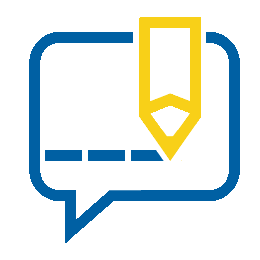

Motor sizing is more than a simple selection. Part one of this discussion explained fundamentals about horsepower (HP), torque and the fan laws. That information will aid in selecting a fan and determine the motor size.
Fan Selection
The fan criteria used for this post was for a direct drive fan with brake horsepower of 0.40. Use a selection tool such as Greenheck’s computer aided product selection (CAPS®) to select a fan that can move 2,200 cfm, against a system pressure of 0.27 in wg. The motor recommended by CAPS is a ¾ hp motor and the selection tool states that the brake horsepower is 0.40 HP. Figure 1 illustrates the fan curve that is provided for the selection.
![]() |
Figure 1 – Fan curve for ¾ hp motor. |
This fan curve provides some needed information. It shows the selected performance point, as noted by the intersection of the system resistance curve (dotted blue line) and the fan performance curve (solid red line). This chart also shows that the fan picked requires the impeller to spin at 1320 RPM to achieve 2200 cfm, and necessitates a 0.4 brake horsepower (shown as a triangle on the HP curve or dotted black line).
Remember, this is a direct drive fan. It will move too much air if the motor is allowed to run at full speed. Therefore, the motor’s speed must be reduced to hit the correct performance.
As the fan speeds up, it moves more air, requiring more HP. This was defined in the first blog on the elements of motor sizing. But it is important to understand that a motor develops HP along with the motor’s RPM. This means that if a motor is not spinning, it basically has no HP, and if it is running full speed it will achieve the nameplate HP. The motor performance graph (Figure 2) reinforces this point. The motor manufacturer provides this type of graph to show a motor’s developed HP at various speeds.Notice that the motor in our example does not provide the full nameplate HP until the motor nearly reaches 1800 RPM.
For this example, the motor needs to spin at 1320 rpm to achieve the desired performance for this fan.
![]() |
Figure 2 |
The vertical red line in Figure 2 shows the point where 1320 RPM hits the HP/RPM curve. Following this intersection, use the scale on the left axis to determine that at 1320 rpm, the motor will provide 0.56 hp. Since the RPM of the fan motor was lowered, the available HP and torque must also decrease.
The 0.56 hp generated is slightly greater than the required brake horsepower for this application. This means that the ¾ HP motor does work in the example, but is it oversized?
Looking at the HP curve for the ½ hp motor (Figure 3), we see that only 0.38 hp is available at the same motor RPM. This motor will not produce the HP needed at the designated RPM.
![]() |
Figure 3 |
Evaluating both motor HP graphs verifies that the ¾ hp motor was the correct size for this fan since it provides enough HP at the specified RPM.
These two blog posts have discussed the topic of sizing motors for fans. It also discussed how the air movement industry typically uses variable torque/variable HP motors. The key takeaway is that these motors will not reach the motor nameplate HP until it has full motor RPM. To generate the required HP at a reduced RPM, the motor must be sized provide the needed HP.
Electronically commutated (EC) motors offer many advantages for fan products including adjusting fan speed, efficiency, cost savings, and less maintenance. Learn more about EC motors and decide which best fits your application.
MotorsRead Next
from